在汽車、電(diàn)子、通信等行業中,線束是連接設備(bèi)與係統的“神經脈絡”,其質量直接(jiē)影響產品的穩定(dìng)性和安全性。而作為線束製造的核心環節,絞線工藝的規範操作直接決定了線纜的(de)導電性、抗幹擾性及耐用性。然而,許多線束廠在實際操作中因流程不(bú)規範導致產品良率下降,甚至引發安全隱患。本文將圍繞線束廠絞(jiǎo)線的正確方法,從(cóng)設備選擇到操作細節,係統梳(shū)理7個關鍵步驟,助您實現高效、高質的生產目標(biāo)。
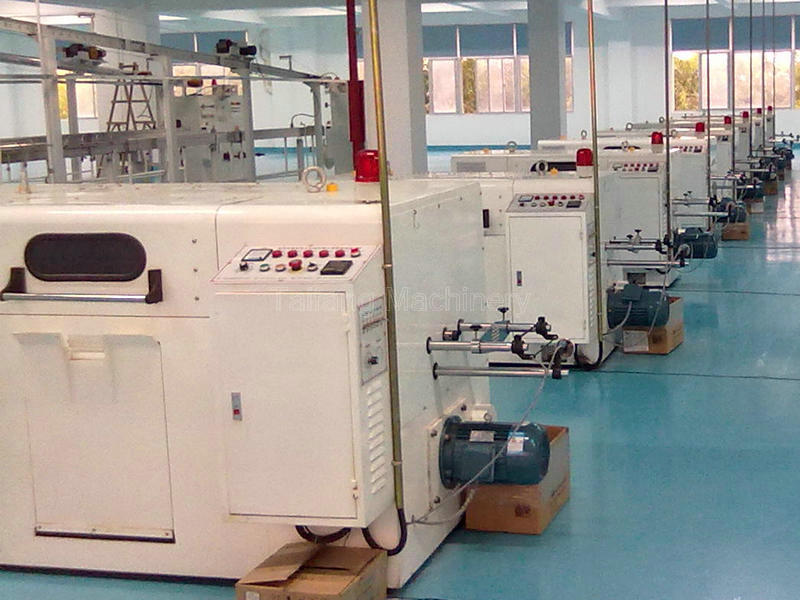
一、絞(jiǎo)線前的準備工作:設備與材料的科(kē)學(xué)匹配
- 設備選型(xíng)與調試
絞線機的性能直接(jiē)影響絞(jiǎo)合效果。需根據線材直徑、絞合節距等參數選擇扭矩穩定、轉速可調的機(jī)型。例如,細線(0.1-0.5mm²)適合使用高速精密絞(jiǎo)線機,而粗線(10mm²以上)需搭配大功率設備。調(diào)試時,需重點檢查絞合模具的同心度,避免因偏移導致(zhì)線(xiàn)芯磨損。
- 材料預處理
*導體退扭*是絞線前的必要步(bù)驟。單絲若存在內應力,絞合後易回彈(dàn)變形。可通過退扭機或自然(rán)懸(xuán)掛方式釋放應力。同時,檢查(chá)絕緣層是否均勻,避(bì)免因厚度(dù)不均導致絞合後外徑波動(dòng)。
二、絞(jiǎo)線操作的核心步驟
- 絞合節距的精準(zhǔn)控製
絞(jiǎo)合節距(即單線(xiàn)螺旋一周的軸向長度)是影響線纜(lǎn)柔韌性與電阻的關鍵(jiàn)參數。經驗公式為:節距(jù)=絞(jiǎo)合外(wài)徑×15~25倍。例如,外徑2mm的線束,節距宜控製在30-50mm。實際操作中需通過試絞調整至最佳值(zhí),並用卡尺實時監(jiān)測(cè)。
- 張力均衡與同步放線
多根單線絞(jiǎo)合(hé)時,若(ruò)張力不(bú)均(jun1)會導致線芯鬆(sōng)散或斷裂。建議使用主動放線裝置,通過傳感器動態調節各線軸的張力。例如(rú),某日企生產(chǎn)線通過閉環控製係統將張力(lì)誤差控(kòng)製在±5%以內(nèi),顯著(zhe)提(tí)升了絞線緊密度。
- 絞向(xiàng)與層數的合理設計
*絞向*分為左向(xiàng)(S絞)和右向(Z絞),多層絞(jiǎo)線需交替(tì)使用以抵消扭矩。例如,內層采用S絞(jiǎo),外層則(zé)用(yòng)Z絞,可減少(shǎo)線束扭曲。對於屏蔽層或高柔性需求場景,可增加絞合(hé)層數至3-4層。
三(sān)、絞線後的質量(liàng)檢驗與問題處理
- 關鍵(jiàn)指標的檢測方法
- 電(diàn)阻測試:使用微歐計測量(liàng)單位長度電阻,偏差超過5%需排查導體純度或絞合緊密度問題。
- 外觀檢查:通過放大鏡觀察表麵是否有毛刺、壓痕,並用千分尺檢測絞合外徑是否符合公差(chà)(通(tōng)常為±0.02mm)。
- 抗拉試驗:模擬實際使用場景,對絞線(xiàn)施加1.5倍額定拉力,持續1分鍾後檢查是(shì)否斷裂或變形。
- 常見問題與解決方案
- 鬆散絞合:多因節距過大或張力不足,可縮短節距並校準放線張(zhāng)力。
- 跳股或斷線:檢查導輪(lún)是否卡頓,或單線表麵存在劃傷。
- 截麵不圓(yuán)整:需更換絞合模具或調整絞合角(jiǎo)度至30°-45°。
四、工(gōng)藝優化:從經驗到數據的(de)升級
隨著智能製造的發展,*基於大數據的絞線工藝優化*成為趨勢。例如,某德係汽車線束廠通(tōng)過采集設備振動、溫度(dù)、轉速等數據,建立(lì)AI模型(xíng)預測絞合缺陷,使不良率(lǜ)從1.2%降至0.3%。此(cǐ)外,引入MES係統(製(zhì)造執行係統)可實(shí)時監控生產參(cān)數,自動生成工藝(yì)改進建議,大(dà)幅提升標準化水(shuǐ)平。
通過上述7個步驟的係(xì)統實施,線束廠不僅能(néng)提升絞線效率,更(gèng)能確保線纜在複雜環(huán)境中的可靠性與壽命。從設備調試到工藝創新(xīn),每一步的精細化管控都是贏得(dé)市場競爭力的基石。
TAG: