在塑料加工領域,PVC擠出機的高效運行直接決定了(le)產品質量與生產效率。然(rán)而,許多操作人員(yuán)在實際生產中(zhōng)常因參數設置不當,導致產品出現表麵粗糙、尺寸(cùn)偏差甚至設備損壞等問題。掌握溫度、螺杆(gǎn)轉速、壓力(lì)等(děng)核心參數的調節技巧,不僅(jǐn)能提升(shēng)成品(pǐn)率,更能延長設備(bèi)壽(shòu)命——這正(zhèng)是每位(wèi)工程師必須精通的”基本功”。
一(yī)、溫度控製:擠出工藝的”生命線”
PVC材料的加工特性決定了溫度敏感性。擠(jǐ)出機通常分為(wéi)進料段、壓(yā)縮段、熔融段和均化段,每個區域(yù)的溫度設定需遵循”梯度升溫”原則:
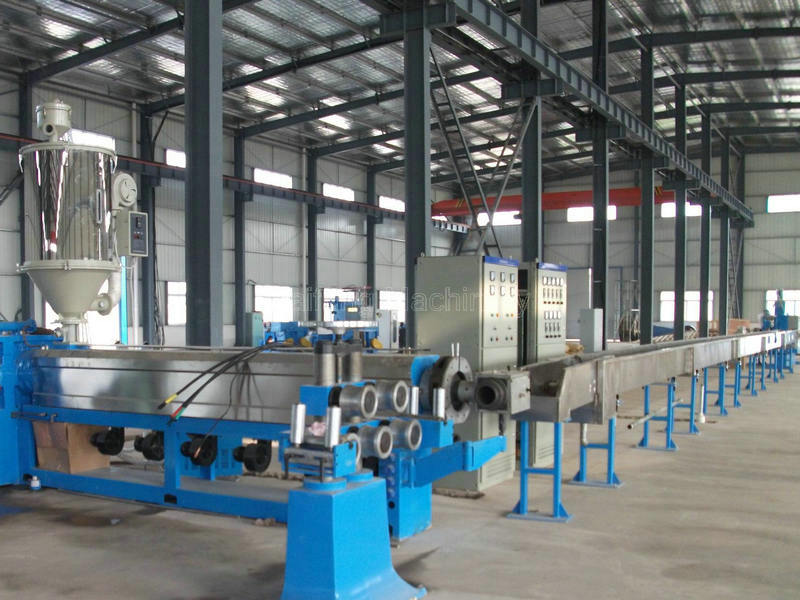
- 進料段(duàn)(160-170℃):溫度過高會(huì)導致原料過(guò)早塑化堵塞進料口,溫度過低則影響輸送效率(lǜ)
- 熔融段(180-190℃):此階段(duàn)需(xū)完全熔融PVC顆粒,溫度波(bō)動超過±3℃即可能引發分解反應
- 模頭段(175-185℃):適當降(jiàng)溫可穩定產品定型,但需與冷卻係統形成(chéng)協同效應
典型案例:某管材生產企業通過將(jiāng)均化段溫度從(cóng)195℃降至185℃,成功將氣泡缺陷率從12%降至1.8%。
二、螺杆(gǎn)轉速:速度與質量的平衡藝(yì)術
作為擠出機的心(xīn)髒(zāng)部件,螺杆轉速直接影響產量與塑化效果。調節時需注意:
- 轉速(sù)與溫度聯動:每提升10rpm,熔體溫(wēn)度可能上升2-3℃,需同步調整加熱係統
- 背壓控製:保持0.5-2MPa背壓可提高塑化均勻性,但超過3MPa會加速螺杆磨損
- 產量公式:Q=πD²hN/4(D螺杆直徑,h螺槽深度,N轉(zhuǎn)速)可作為理論參(cān)考(kǎo)值
黃金法則:對於φ65mm螺杆,生產3mm壁厚管材時,建(jiàn)議(yì)轉速控製在25-35rpm區間(jiān)。
三、模具(jù)壓力:決定產品精度的”無形之手”
模頭(tóu)壓(yā)力調節常被忽視,卻(què)是(shì)影響產品尺寸穩定性的關鍵因(yīn)素:
- 壓(yā)力監測:安裝熔體壓力傳感器(qì)(建議量程0-40MPa)
- 調節技巧:
- 通過口模平直段長度調整:每增加10mm長度,壓力提升約15%
- 采用阻流塊微調:可(kě)改變局部熔體流速分布
- 預成型板優化(huà):將(jiāng)開孔(kǒng)率(lǜ)控製在60-70%可平衡(héng)壓力與流(liú)速
某型材生產企業通過優化模具壓縮比(bǐ)(從3:1調整為2.5:1),使(shǐ)角線接縫問題減少70%。
四、冷卻係統:容易被低估的關鍵環節
冷卻效(xiào)率(lǜ)直接影響產品結晶度和機械性能:
- 真空定徑箱水溫建議控製在12-18℃,溫差需穩定(dìng)在±1℃以內(nèi)
- 噴淋冷(lěng)卻角度應調整為45°入射,確保管材周向均勻冷卻
- 牽引速度匹配公式:V=Q/(ρ×A)(Q擠出量,ρ材料密度,A截麵積)
注意:過快的冷卻會(huì)導致內應力積聚,建議采用”梯(tī)度降溫”法,第一段冷卻(què)水溫比後續段高5-8℃。
五(wǔ)、參數聯動:係統化調(diào)整策略
擠出(chū)工藝本質是多參數耦合係統,建議建(jiàn)立以下調整流程:
- 根據(jù)配方確定(dìng)基礎溫度曲線
- 以60%額定轉速啟動設備
- 觀察熔體壓力波動是否在±5%範圍內
- 通過在線測徑儀(yí)實時反饋調(diào)整牽(qiān)引速度(dù)
- 每調整(zhěng)一個(gè)參數後,需穩定運行15分鍾再記錄數據
某薄(báo)膜生產(chǎn)企業通過引(yǐn)入MES係統,將參數調整時間從3小(xiǎo)時(shí)縮短至45分鍾,廢品(pǐn)率降低40%。
六、常(cháng)見問題快速診斷表
現象 |
可能原因 |
解(jiě)決方(fāng)案 |
表麵鯊魚皮 |
熔體溫度過低 |
提升模頭段溫度3-5℃ |
軸(zhóu)向條紋 |
螺杆轉速過高 |
降低10-15rpm並檢查濾網 |
截麵橢圓 |
冷卻不均勻 |
校準真(zhēn)空箱(xiāng)水位(wèi)與噴淋角度 |
顏色發黃 |
局(jú)部過熱分解(jiě) |
檢查加熱圈(quān)接觸與熱電(diàn)偶精度 |
掌握這些核心參數的調節邏輯,就能讓PVC擠出機從”能用(yòng)”變為”好用”。隨著智能控製技術的普及,參數優化正從經驗驅動轉向數據驅動,但基礎原(yuán)理的深刻(kè)理(lǐ)解始終是技術(shù)升級的基(jī)石。
TAG: